Eko Okna: An automated manufacturing process managing 6,000 daily orders across 5 production halls
Using Sheetgo, Eko Okna now saves 11 days per month with a custom manufacturing workflow that simultaneously creates work schedules and purchases material needs.
As a result, their complex order system is now a simple workflow that they can easily share with suppliers and the production team.
Manually organizing data from a complex database
- Complex system required high-volume data transfer
- Tedious manual extraction of CSV data to Google Sheets
- Tricky sharing specific data with production team and suppliers
As the project manager, Dawid’s job involves collecting orders and using this data to calculate two different things: the number of working hours needed for the production team to carry out the order, and the materials needed from suppliers to fulfill the order.
Before reaching out to us, Dawid had to do the entire process manually. He would manually transfer information from the database to CSV files. Then, he would go through each row of data and extract the working hours to move into a new spreadsheet for his production team, and then extract the materials data into a new spreadsheet for his suppliers.
Dawid would have to do this for around 6,000 rows of data per day, as this was the average number of daily order requests. In order to speed up production and minimize errors, Dawid needed a solution that would automate this process from start to finish.
By using Sheetgo, Dawid realized he could turn this complex process into a simple, self-sufficient solution that would free up a huge amount of his working day.
An automated order process to fulfill thousands of national orders
- Turning a complex database into 83 ready-to-share files
- Merging data to correct process and location automatically
- Accessible to staff on 50 touchscreens in the production hall
With Sheetgo, Dawid was able to create a simple yet powerful workflow that would merge the data from his CSV files into the corresponding spreadsheets, so that the production team and suppliers would receive their information without Dawid needing to lift a finger.
First, Sheetgo uses the Merge feature to add all the CSV files into a folder. Then, using 2 connections with filters, the estimated hours data is extracted and stored into the production master sheet, and the materials data extracted into the supplier master sheet.
The data from the production master sheet is then split according to the production hall. Each tab contains the specific working hours data assigned to each department within the hall. Here, the production team has access to all the information they need. The data from the supplier master sheet is also uses the Split feature to divide material information by supplier.
Suppliers have access to purchasing materials information. From here, Dawid can also schedule automatic updates for the entire workflow, so that both the production team and suppliers receive the latest order information every single working day.
Saving 11 days per month to focus on order fulfillment
- 1079 hours saved every year
- 11 days of work saved every month
- Complete data control through specific data sharing
Thanks to this new automated process, Dawid no longer has to manually transfer thousands of order requests into various spreadsheets to manage the production and supply lines. As a result, Eko Okna saves up to 11 work days per month.
With this automated system custom designed by Sheetgo, Dawid is able to supervise the data transferral of thousands of orders to 3,500 production workers across 5 different locations simultaneously.
Now, Eko Okna has a fully automated manufacturing process that allows for reliable and efficient planning and production.
In addition to saving time, the company now has a flexible spreadsheet-based system which Dawid can easily add to or adjust as demand grows and the company inevitably expands.
Eko-Okna is Europe’s largest producer of aluminum and uPVC windows, doors, and shutters. With manufacturing facilities located in southern Poland, Eko-Okna employs a total of 7000 people at its sites across the country. 3500 people work at the 5 production halls, manufacturing 6000 windows every single day.
Poland
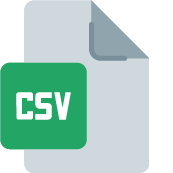

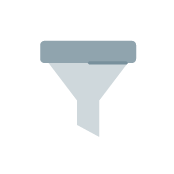
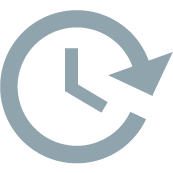