HMG Healthcare: An automated and flexible inventory solution to solve critical COVID-19 demands
Fulfilling critical COVID-19 demands via spreadsheets
- High-demand PPE requests for staff in 30+ locations
- Complex inventory with over 40,000 items
- Hard to track multiple vendors and fluctuating prices
With the outbreak of the COVID-19 pandemic, HMG faced the challenge of acquiring and distributing personal protective equipment to care staff, as quickly as possible. Global demand made this task more complicated, as HMG had to buy these products from multiple vendors at fluctuating prices. At that time, they were using Excel spreadsheets and manually managing procurement and inventory, which was becoming an extremely time-consuming process.
The new demands imposed by the pandemic made this system unsustainable, and HMG desperately needed an alternative solution.
Flexible and dynamic inventory control using Sheetgo
- Custom-built inventory management solution
- Two-way sync data transfer to speed up supply chain
- Automatic updates for the latest inventory insights
With Sheetgo, HMG has created a custom, automated inventory workflow based on Google Sheets. Now their data is clearly divided into two spreadsheets; one containing order requests, and another containing the purchases.
With a two-way sync from their ‘Main Inventory’ master sheet, Sheetgo automatically determines whether an order can be placed based on PPE availability. If so, the request is approved, and this order is sent directly to the ‘Purchases’ file. With this synchronisation, the team always have the latest updates, including PPE order confirmation and delivery status.
Saving 20+ hours per week with a self-sufficient system
- 1120 hours saved every year
- 20+ hours saved every week
- 100% up-to-date inventory metrics
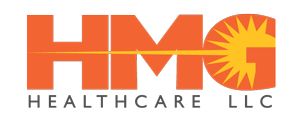
Based in Texas, HMG Healthcare manages 30 specialist nursing and rehabilitation facilities across the US. The company uses a data-driven approach to understand predictors and seeks to improve quality of care using analytics to prescribe the right course of treatment.
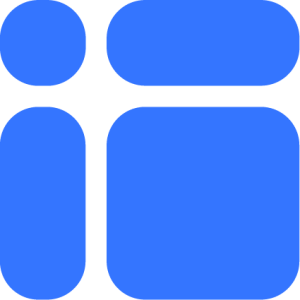
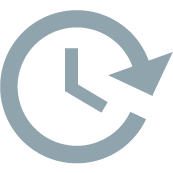