Tactile Knife: Automated inventory stock control using Sheetgo
Tactile Knife is a highly regarded Texan knife manufacturer specializing in high-end products.
They use Sheetgo to manage inventory, purchasing and sales, which saves them 3 hours of work every single day whilst also eliminating overselling issues from their business.
A need to automatically track inventory across multiple teams
- Two teams and 20 technicians need accurate inventory
- Integrate scanning guns with spreadsheet data
- Eliminate overselling issues across multiple lines
Their existing scan gun system was outdated, not integrated effectively with their spreadsheets, and was leading to a consistent overselling problem.
“Feedback from all employers has been great.”
Mike Palmore, Assembly Manager at Tactile Knife
The assembly manager connected with Sheetgo after searching for how to connect scan guns with Google Sheets. He wanted a solution with minimal coding that would be operationally ready and easily accessible for a wide-ranging team.
Without being able to quickly track each part with a scan gun, they were facing delays in production times and targets as they expanded.
Automated inventory scanning using Sheetgo
- Automations provide multiple checkouts for 20 technician inventories
- 3 staff oversee Sheetgo, predominantly with Merge and Filter tools
- Sheets load faster due to less reliance on DIY formulas
Sheetgo allows Tactile Knife to automate the personal inventories of each of their 20 technicians while also maintaining a central inventory in real time.
The process of consolidation is overseen by 3 dedicated members of their team who work with Sheetgo throughout the day. The entire tream has given very positive feedback and they were able to adopt Sheetgo quick and easy.
“Love filter for multiple inventories.”
Mike Palmore, Assembly Manager at Tactile Knife
Sheetgo allows Tactile Knife to save 3 hours per day for both of their teams. They are also able to 100% eliminate their previous problem of overselling by tracking inventory in real time.
Scanning rates and accuracy have also improved thanks to the ability to automatically connect sheets with Sheetgo.
Tactile Knife now saves 1,500 hours a year!
- 6 hours of time saved across two teams daily
- Full adoption by all 20 technicians and craftsmen
- Bills of materials readily available across multiple products
By using Sheetgo, the knife manufacturing team is able to save up to 1,500 hours a year that they can devote to higher value tasks.
They were able to successfully roll out the same solution, with minimal changes, to fit their pen production processes as well. The team achieved this while reducing overselling to zero.
“Manually counting the inventory of each technician (counting all the little bits and pieces in their heads) took hours.”
Mike Palmore, Assembly Manager at Tactile Knife
By implementing Sheetgo, Tactile Knife has saved 1,500 hours a year. This equates to approximately 190 working days that can be better spent on high-value manufacturing processes. Overselling has been 100% eliminated by safeguarding against manual entry errors.
The end result is a business with an automated and integrated approach to managing all data associated with inventory, purchasing and sales functions.
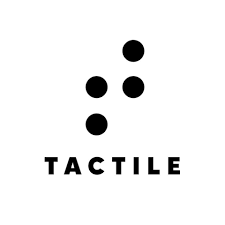
Tactile Knife is a Texas-based machine shop producing high-performance knives backed by a lifetime warranty. They believe in artisan craftsmanship and the use of premium materials as standard.
TX, USA
Industry
Manufacturing
Features used
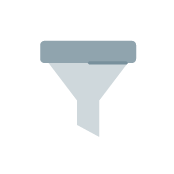
